Solid waste grinding and sorting
Classifying and Ball Mill
Production Line
Classification Principle ofClassifying and Ball Mill Production Line
According to the principle of superfine ball milling classification, through redesigning and arranging the traditional ball mill lining plate, grinding body and discharge device, the ordinary ball mill is upgraded to superfine ball mill, and then combined with the Special Superfine Classifier to form a closed-circuit system, which can superfine grind the steel slag, slag, fly ash, desulfurization gypsum and other industrial waste to a specific surface area of more than 700, The energy consumption per ton of product is less than 50 kwh.
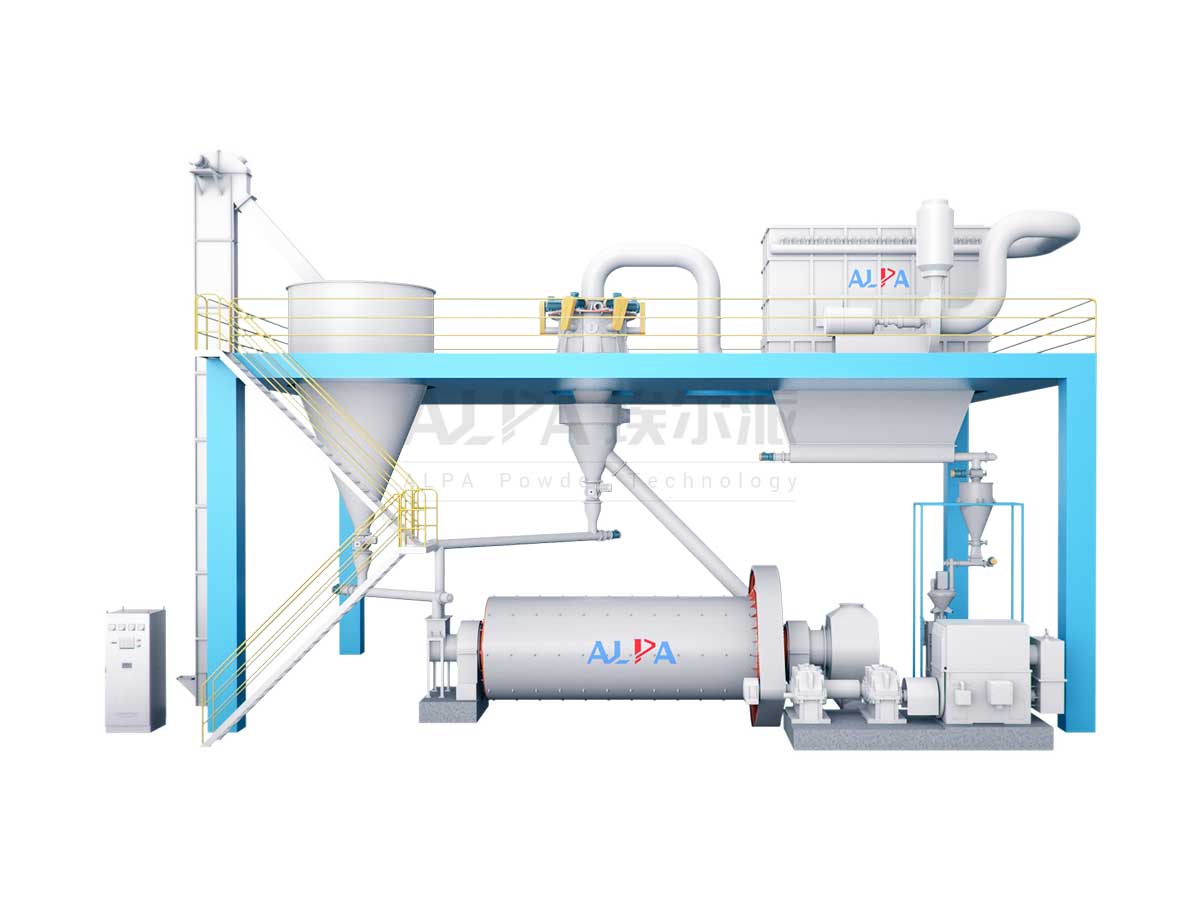
Advantages of Solid Waste Processing by Classifying and Ball Mill Production Line
- Fly ash can be ground and separated-grade ash, ultra-fine ash, specific surface area 400-2000m²/kg;
- Fly ash can be separated and extracted from 2-45μm ultrafine beads, which can be used as rubber and plastic fillers instead of calcium carbonate;
- Fly ash can be separated and extracted 2-15μm ultra-fine beads, which can be used as a water reducer or mineral admixture to replace silica fume, etc.;
- Steel slag and slag can grind S75, S95, S115, S125 and other varieties, with a specific surface area of 400-3000m²/kg;
- Large processing capacity, high classification accuracy, fine product particle size;
- The equipment is wear-resistant, negative pressure throughout, energy saving and environmental protection.
Application: Fly ash, slag, steel slag, tailings, lean ore, red mud, etc.
Major Equipment of Ball Mill Grading Production Line
Ball mill
- The ratio of length to diameter of ball mill is optimized to provide more ideal output and fine powder rate, avoid excessive grinding and improve grinding efficiency;
- The size of grinding cavity and opening are optimized. Feeding and discharging are smooth, no need cooling pipe;
- The lining plate and grinding medium are manufactured according to German standards, which extend the service life of the grinding medium and improve the wear resistance. According to the requirements of product fineness, the size and material of grinding medium are designed to improve the grinding efficiency;
- The grinding energy consumption is reduced to the greatest extent, and the energy and operation cost are saved.
Control system
- PLC control, high degree of automation, easy to operate; easy to integrate with other system programs, easy to manage;
- Both the material silo and product silo have leveler, which can realize automatic control of the entire production line;
- Touch screen man-machine interface, convenient process control and adjustable parameters.
Quantitative system
- Ball mill feedstock adopts a precise quantitative system, which can stabilize the feed even if the density of the material changes;
- Classifier feedstock adopts a precise quantitative system and interlocks with the discharge of the ball mill to ensure the stability of the system operation and product granularity;
- High-precision metering pump, according to fineness requirements of product, spray the grinding aid into the mill with accurate time and dosage;
- The damper valve has an airflow measurement system that allows accurate control of the flow volume and rate of classifying.
Environmental protection and noise control
- The whole system operates under negative pressure, and there is no dust overflow, realizing clean production;
- Adopt efficient muffler, exhaust noise<80dB(A);
- All heavy-duty moving parts have shock absorbers;
- There is no waste water discharge.
Classifier
- Originated from German technology, it is divided into vertical turbine classification and horizontal turbine classification;
- Accurate frequency conversion control ensures perfect classification accuracy;
- The structure of the classifier is optimized, the path of material and air flow is more reasonable, the air volume of classification is adjustable, the classification efficiency and flexibility are improved;
- The new NG rotor design improves the classification accuracy, reduces the resistance and reduces the energy consumption.
Main Equipment Specifications and Parameters of Ball Mill Classifying Production Line
Ball mill model | IBM1830 | IBM2200 | IBM2400 | IBM2600 | IBM2800 | IBM3000 | |
Boll mill power (kW) | 220 | 320 | 450 | 630 | 710 | 800 | |
Classifier | Model | 1 machine FW630/4 | 1 machine FW630/6 | 2 machine FW630/4 | 1 machine FW630/6 | 1 machine FW800/4+1 machine FW800/6 | 2 machine FW800/6 |
Power (kW) | 192 | 290 | 384 | 580 | 670 | 764 | |
Auxiliary equipment power(kW) | Crush system | 37 | 55 | 65 | 90 | 90 | 110 |
Conveyor packaging | 11 | 22 | 22 | 30 | 37 | 37 | |
Air compressor | 18.5 | 30 | 45 | 55 | 75 | 90 | |
Particle size and productivity(t/h) | D97:15μm | 2.7 | 4.0 | 5.4 | 8.0 | 9.4 | 11 |
D97:10μm | 2.0 | 3.0 | 4.0 | 6.0 | 7.0 | 8.0 | |
D97:5μm | 0.9 | 1.3 | 1.8 | 2.7 | 3.0 | 3.6 |